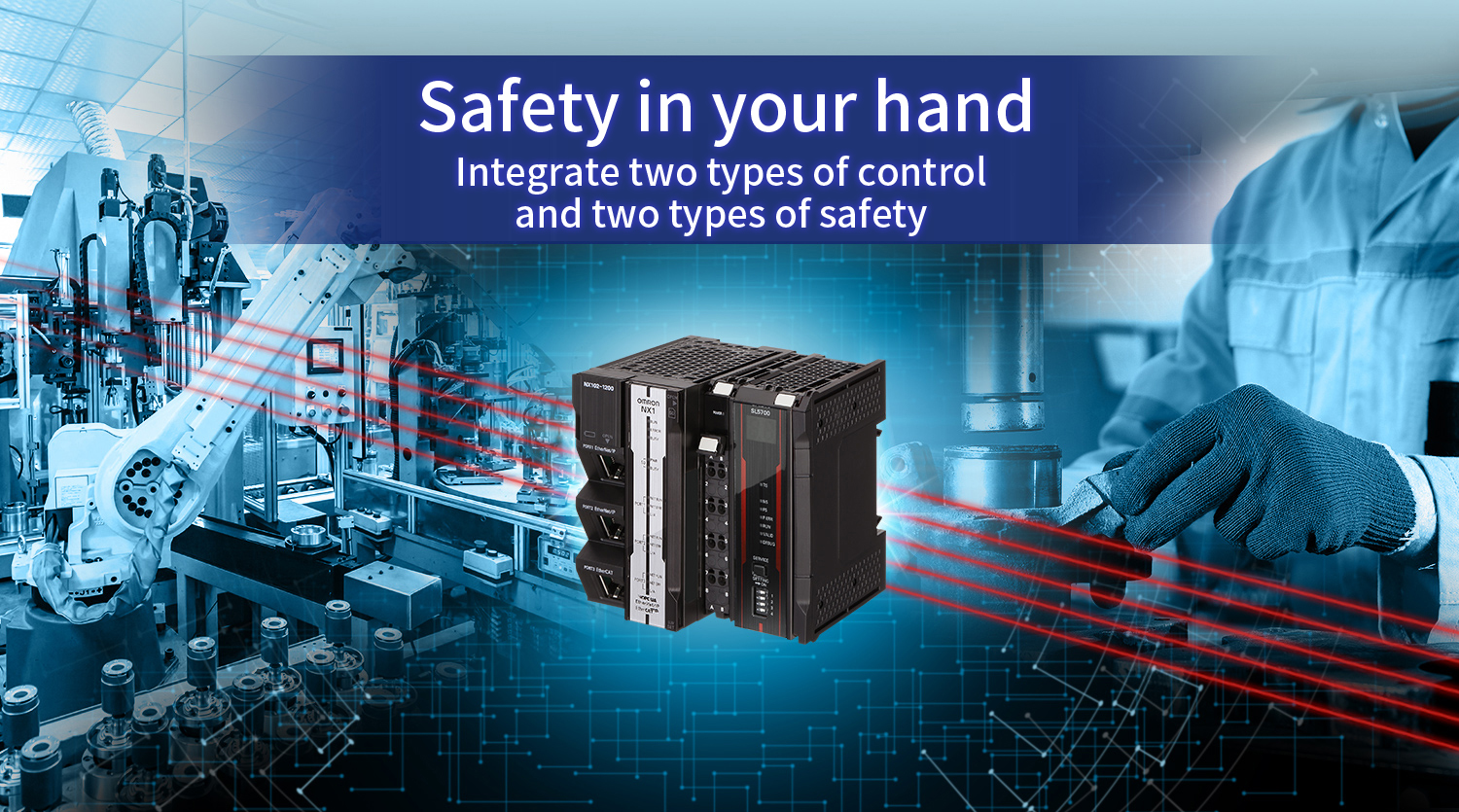
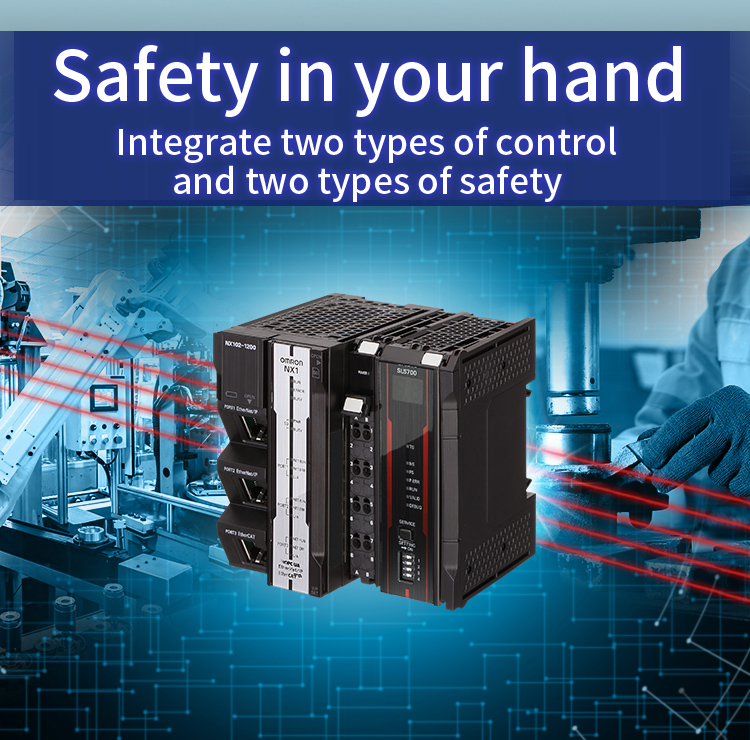
The NX1 Controller is the first in the world* to integrate two different open networks:
EtherNet/IP™ + CIP Safety™for scalable safety control of production lines and EtherCAT® + Safety over EtherCAT (FSoE) for fast safety control of machines.
This integrates safety control into machine control in lines that require fast cycle times.
* Based on Omron investigation in March 2018.
Conventionally safety control and machine control are performed in different networks. The use of Safety over EtherCAT (FSoE) allows the NX1 Controller to use a single communication system, EtherCAT, for both safety control and machine control.
This enables management of both the control and safety systems at once, which were previously performed separately.
Automotive parts stamping requires safety measures because even manufacturing of small parts carries risks. However, it takes time and effort to install a different controller for safety components from a standard controller. The NX1 provides both machine control and safety control using a single EtherCAT network.
Previously, the integration of machine safety functions into manufacturing process control required a lot of work. It was difficult for users to integrate production control and safety control by themselves when they had no specialists in safety. They had to outsource installation to safety device manufacturers or engineering companies.
Addressing this challenge, we developed the NX-SL5 Safety CPU Unit supporting CIP Safety that adds safety functionality to the open network EtherNet/IP. The NX102 CPU Unit has built-in EtherNet/IP ports that enable CIP Safety connections.
This allows users to upgrade or add safety devices to their existing EtherNet/IP network systems.
In an automotive parts assembly process, management of both control and safety is crucial to cell production where robots work. The NX-SL5 Safety CPU Unit can connect to industrial robots and various safety devices via CIP Safety. New functions are added to the Sysmac Studio to improve design efficiency and productivity during the safety control program creation phase. Functions such as Automatic Programming and Safety Data Logging now can be used, and control of a manufacturing process can also be integrated.
NX1 Machine Automation Controller